Maximising Technology in Metal Pressings & Stampings Manufacture
An Overview of How Technology Benefits Pre-Met
In this article, we explore how technology is maximised in the world of metal pressings and stampings at Pre-Met Engineering. Technology is leveraged at all stages from design to supply chain management. Let’s find out more.
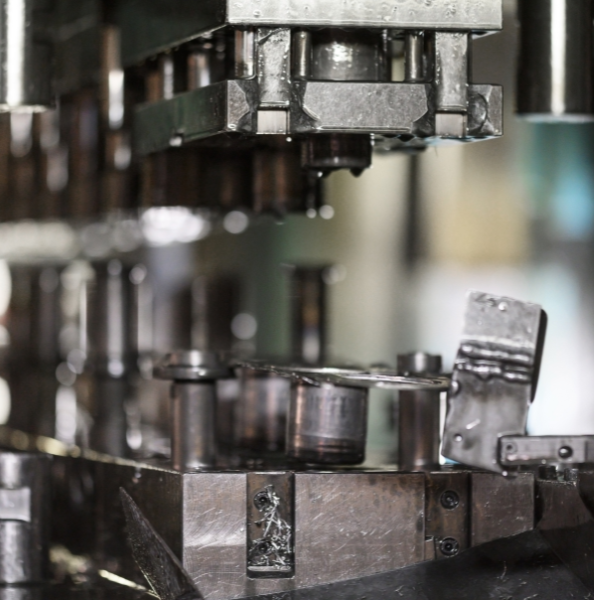
Technology and Engineering
Technology plays a key role in modern engineering. In this latest blog, we examine how technology helps Pre-Met optimise products and services in the following areas:
- Design and Production Efficiency and Cost Savings
- Predictive Maintenance
- Technology Empowers The Workforce
- Tooling and Quality Control
- Supply Chain and Prototyping
- Continuous Improvement, The Kaizen Way
Design and Production Efficiency and Cost Savings
Technology means Pre-Met can optimise material use, reduce waste, and lower the environmental impact. It helps us to refine the design of intricate stamping tools to drive down cost savings and maximise resources. In addition, we can calculate the most efficient layouts for stamping runs with significant cost savings.
Using technology, we can leverage historical data and material characteristics to produce optimised designs. This improves precision, reduces waste to a minimum, and boosts the overall efficiency of production.
Predictive Maintenance
At Pre-Met, we carry out predictive maintenance algorithms that provide proactive equipment maintenance. Real-time data from sensors in the factory help to identify potential failures and then carry out planned maintenance. This reduces the need for costly interruptions by spotting maintenance issues before they go wrong. Therefore, the cost of maintenance is lowered and also reduces downtime in our metal stamping and metal pressing operations.
Technology Empowers The Workforce
In the media, there is a significant focus on how technology is likely to take away jobs in the future. However, advances in sheet metal fabrication technology actually allow workers to achieve greater efficiency, precision, and productivity,
“...does not replace human workers; rather, it augments their capabilities. By automating repetitive tasks and leveraging AI-powered insights, manufacturers empower their workforce to focus on more complex, value-added activities.”
Source:
Mridul Krishna Dey, April 16, 2024
Equally, technology training initiatives are improving the skills and technical knowledge of the workforce. This keeps staff at the leading edge of technological advancements in engineering in an increasingly competitive market.
Tooling and Quality Control
Advanced technology has also been highly beneficial to tooling and die design. It has streamlined tooling quality in processing design elements and production variables. Also, it is possible to make tools more durable and precise. Using simulations, we improve the process, reduce costs, and guarantee high-quality finishes.
Quality control is carried out in real time and ensures product consistency. We have the technology to monitor the metal stamping cycle and immediately spot flagging deviations to stop defects from occurring.
Supply Chain and Prototyping
We maximise technology by utilising it to provide efficient supply chain management as it is able to predict demand shifts, as well as anticipate disruptions. This means we can streamline sourcing and meet our delivery deadlines. Equally, our existing technology speeds up prototyping, using virtual simulations to anticipate component performance under various conditions. Ultimately, this means our market entry times are more rapid and innovation is accelerated.
Continuous Improvement, The Kaizen Way
Harnessing technology, Pre-Met can continuously analyse data, refine processes and make recommendations over time. This contributes to industry best practices, improving efficiency and reducing defects. Continuous improvement is part of the Kaizen philosophy that we follow.
Business Performance Management
Pre-met’s overall business performance has been helped immensely over recent years with the deployment of business metrics. These form an overall dashboard/ scorecards that indicate critical business performance aspects quickly, simply & effectively on a daily/weekly frequency.
Reflections
Here at Pre-Met Engineering, we continuously embrace new technology in our industry to deliver the highest quality products and services possible to all of our clients worldwide.
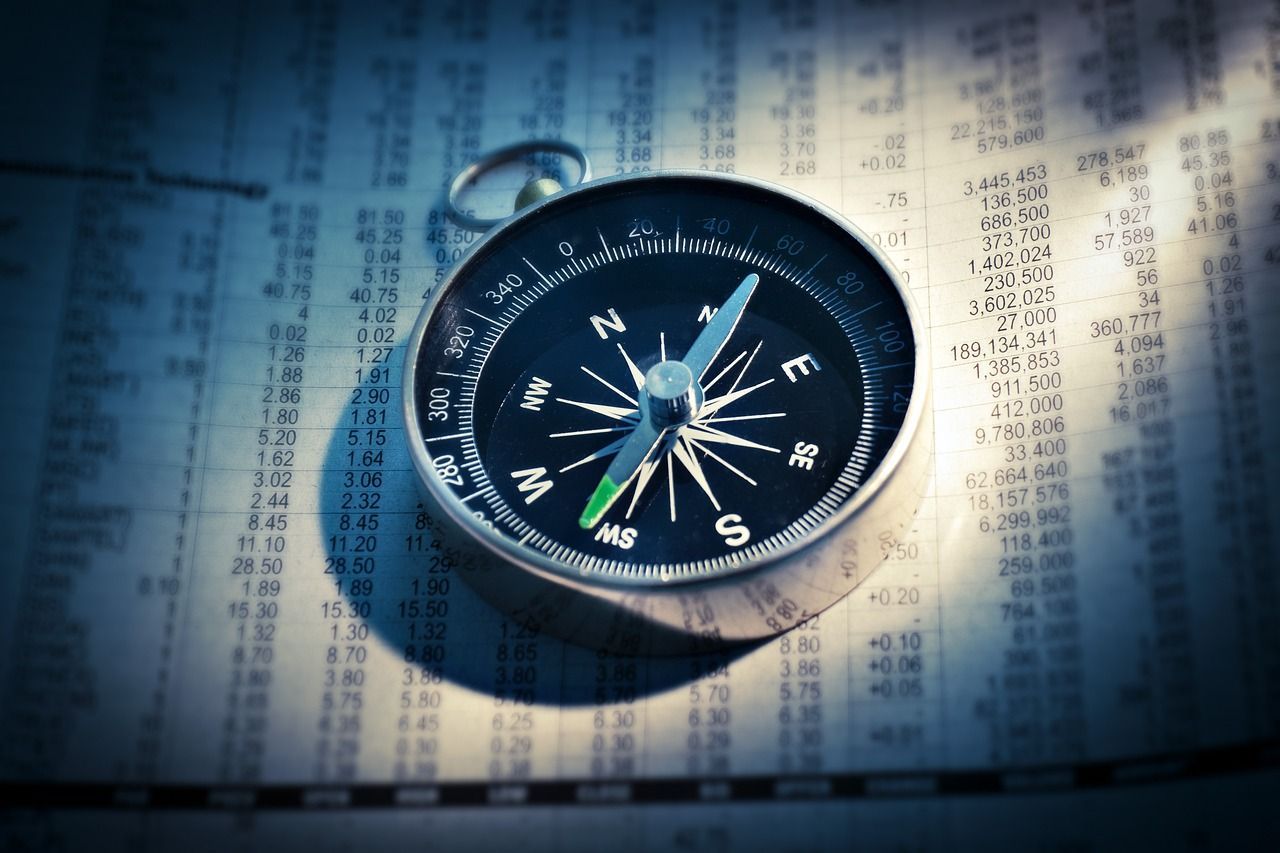
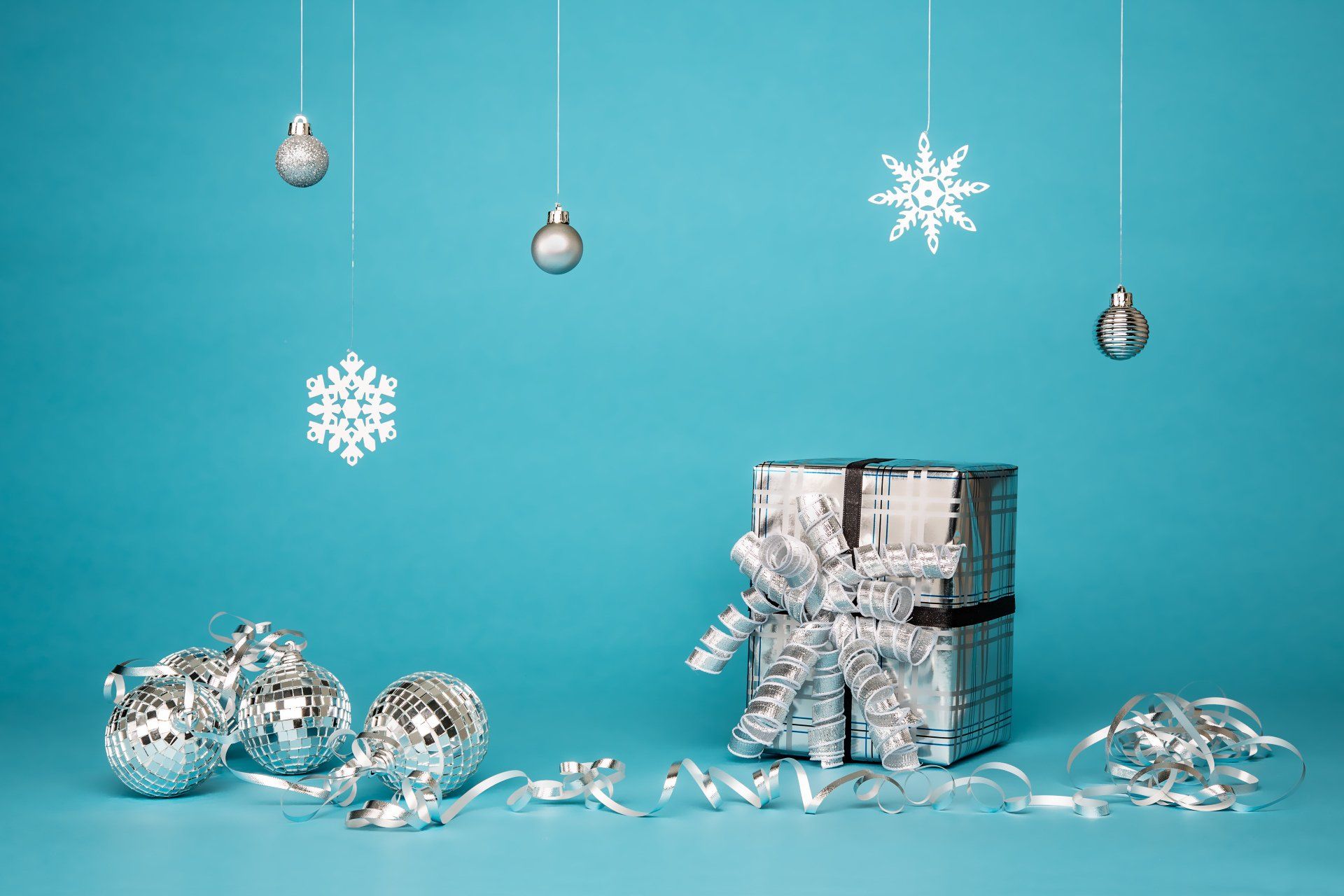
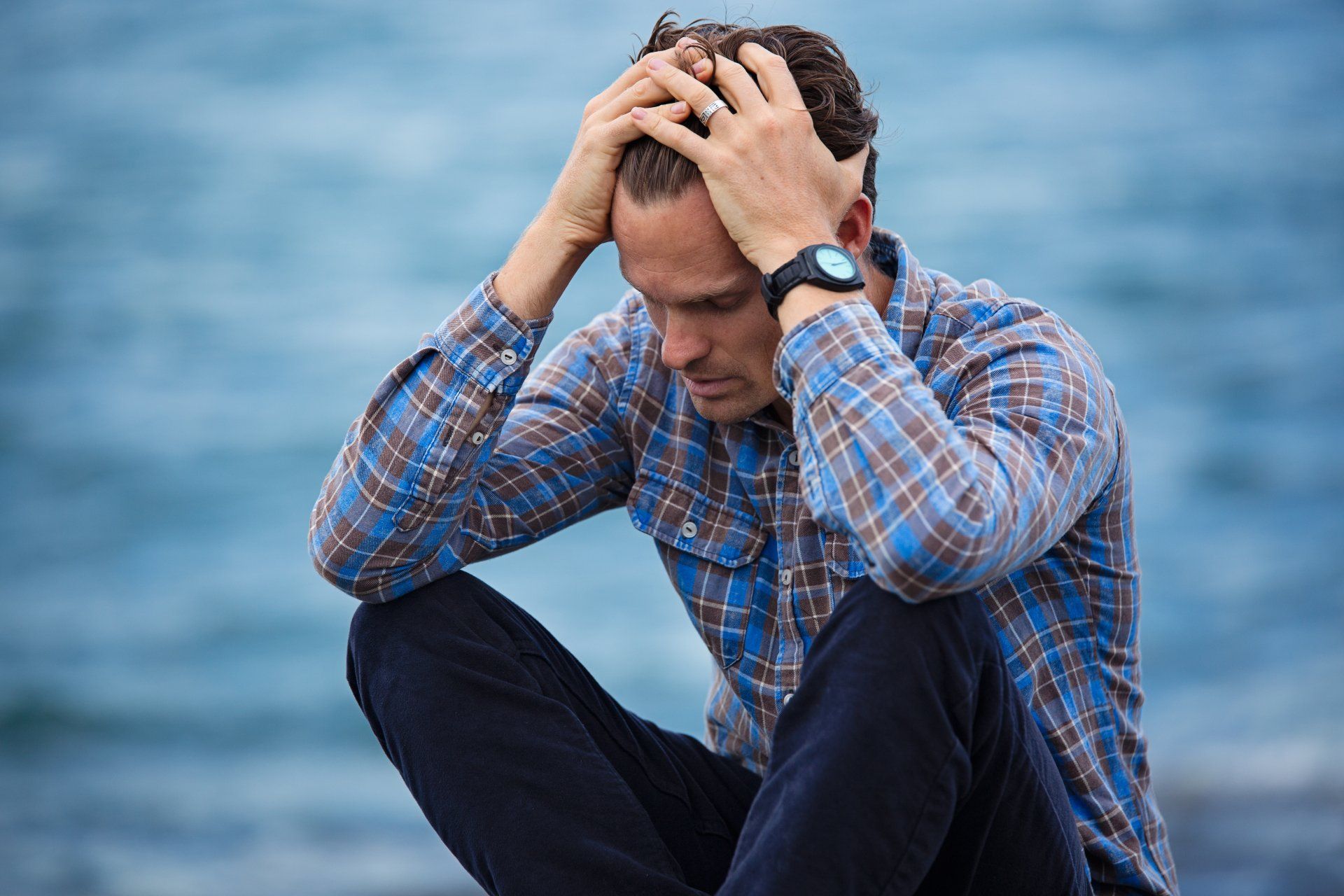
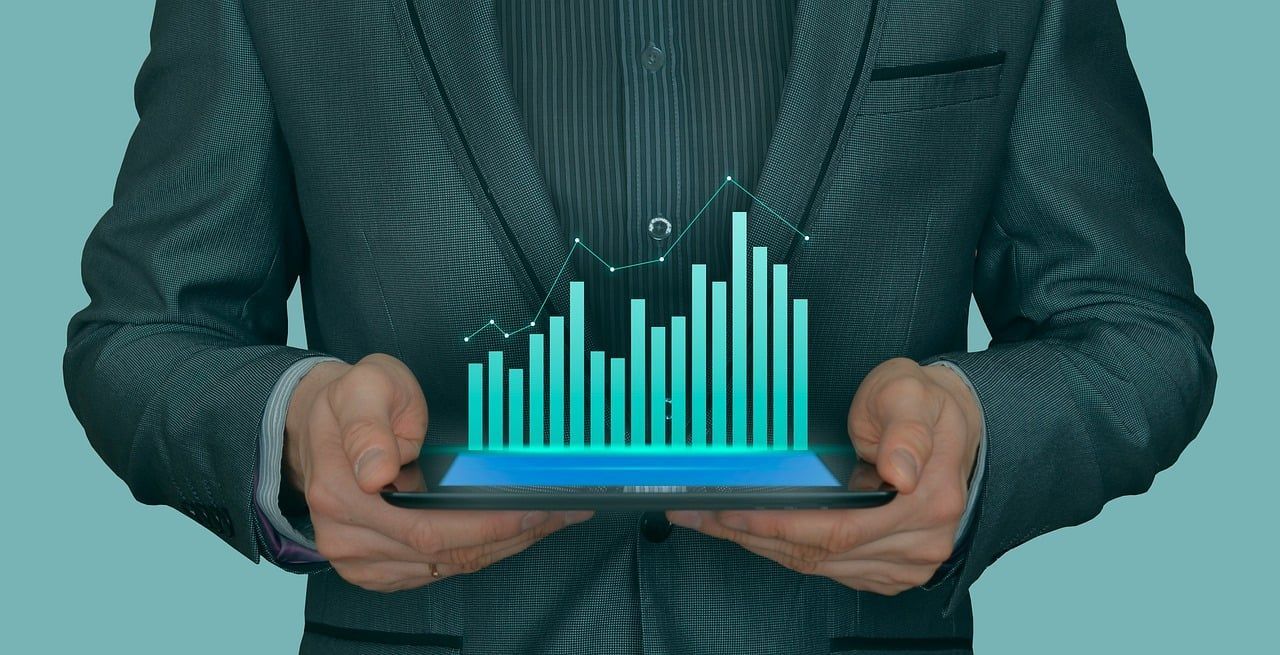
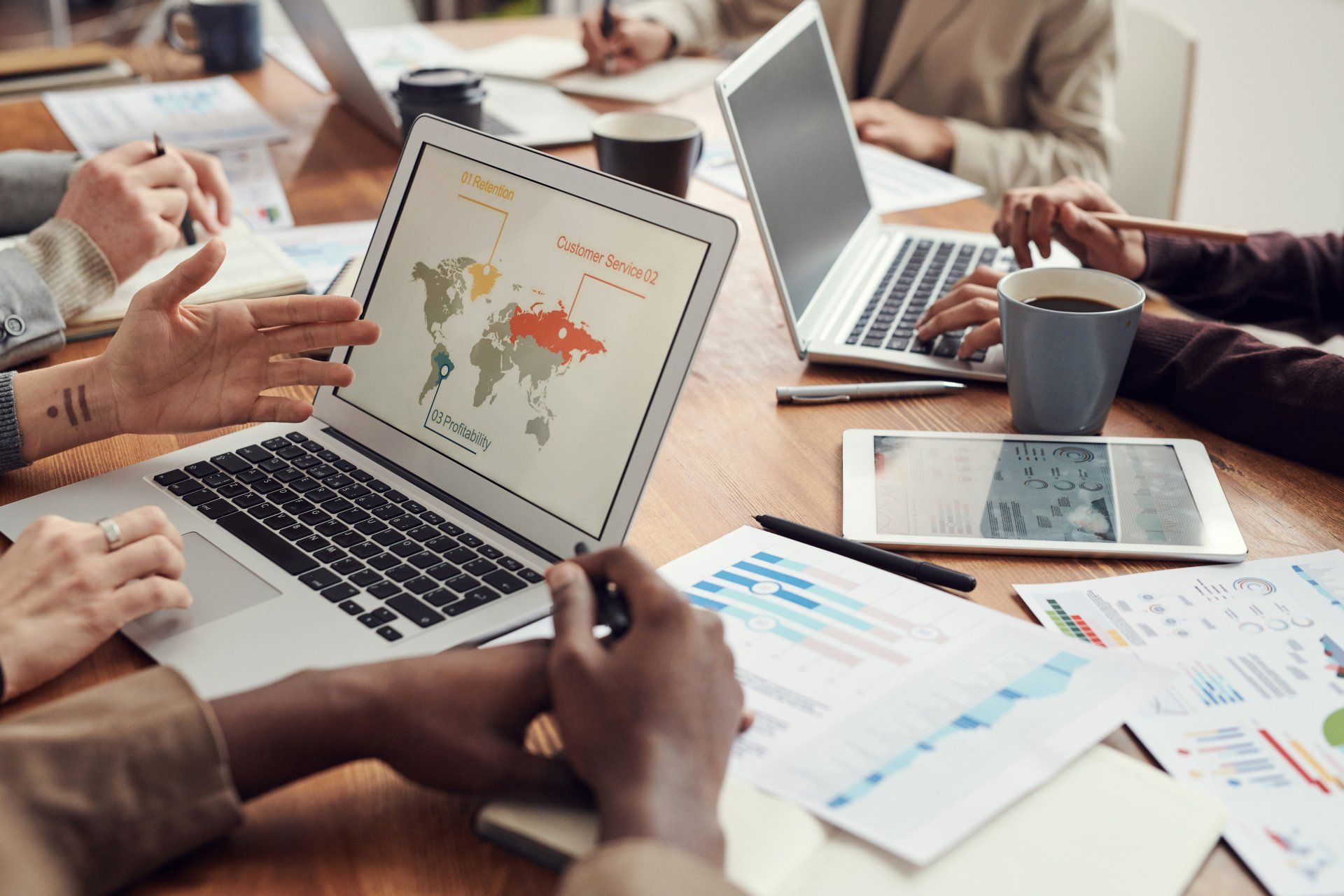
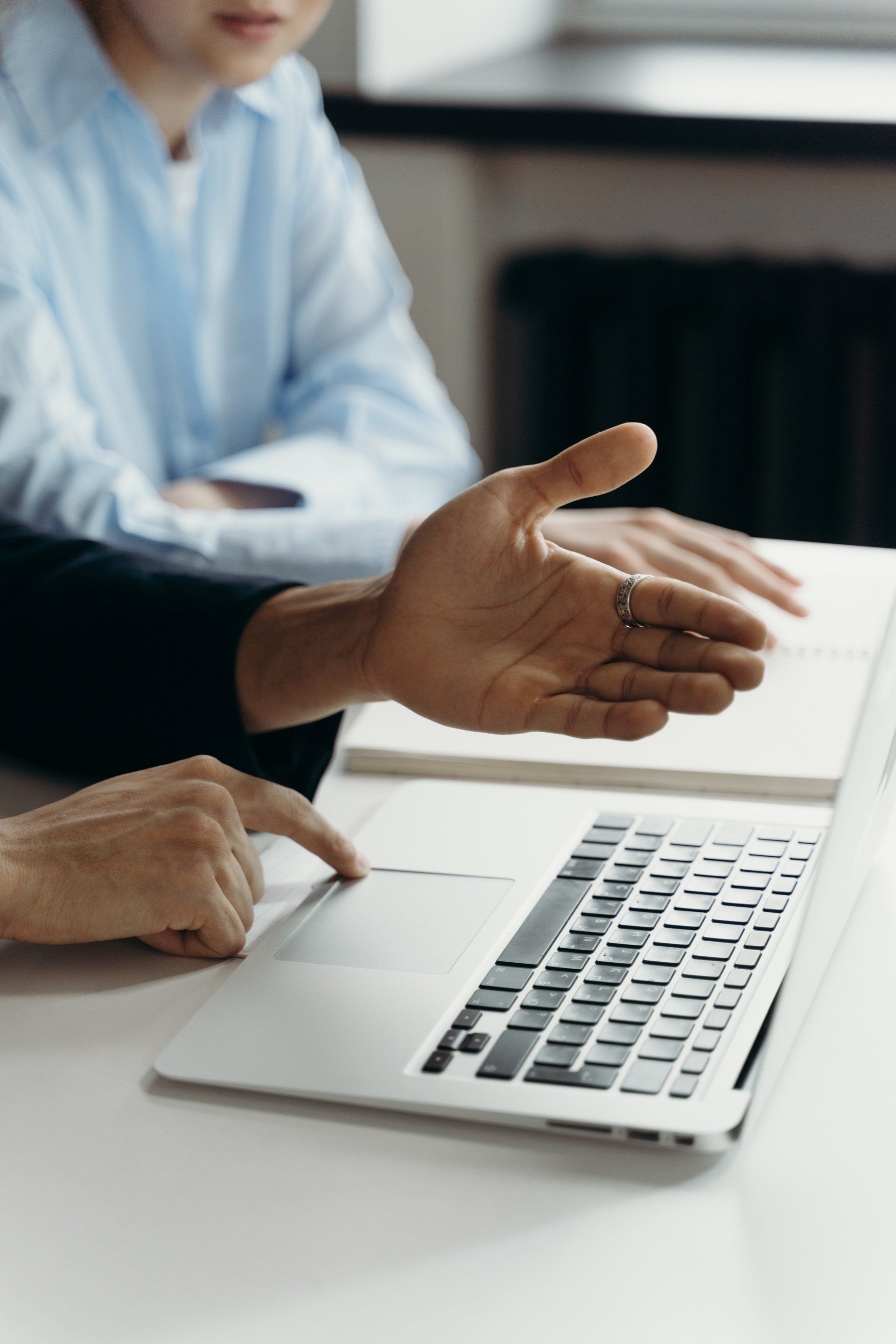